2 Preventive Maintenance
2.1 Introduction
The procedures on the following pages are routine maintenance procedures to be performed on a scheduled basis. These procedures are recommendations that if followed will aid in maintaining system performance and data integrity.
These routines aid in detecting trouble trends and intermittent troubles. As with any maintenance activity, personnel should be encouraged to maintain a log of all routines performed. This aids the maintenance technician as well as My Oracle Support (MOS) in determining the source of system troubles and ways to prevent certain troubles from occurring again.
Instructions for performing required maintenance routines are provided. In the event another document may be required for a specific task, that document is referenced.
2.2 Maintaining the Fuse and Alarm Panel
The Fuse and Alarm Panel (FAP) serves as a central location for identifying a variety of potential problem conditions. However, you may have to occasionally perform corrective maintenance on the FAP, itself.
The FAP consist of five major functions:
- Input connections
- Diodes
- Fuse Arrays
- Alarm circuitry
- Output connections
Figure 2-1 FAP High-Level Block Diagram

To assist your FAP maintenance efforts, this section provides information about the FAP unit:
- The FAP components
- FAP alarms
- Diode testing and the diode jumper
For more detailed information on the FAP and its components, refer to the FAP Technical Reference (820-2888-01).
2.2.1 1U FAP P/N 870-2804-01
The 1U FAP (P/N 870-2804-01) is a low-profile unit that provides protected distribution of –48VDC power to the shelves in the frame. Allowing for the full population of a frame and for the failure of one primary supply, new installations of Control and Extension frames require two 60A feeds.
2.2.1.1 FAP Components
The FAP is composed of three field replaceable units, of which two can be hot-swapped.
Table 2-1 FAP Component Replacement
Component | Replacement Requirements | Part Number |
---|---|---|
Diode Board |
Field replaceable |
870-2806-01 |
Shorting Board |
Field replaceable |
870-2805-01 |
1U FAP |
Field replaceable (with service interruption) |
870-2804-01 (includes Diode and Shorting Boards) |
Diode Board
The diode board in the FAP contains power diodes and circuitry which allow one bus to pick up the entire load when there is a loss of input power on the other bus.
Shorting Board
The Shorting board allows the removal of the diode board without taking down the system. This permits periodic maintenance of the diodes without having to power down or remove the unit from the shelf. In the bypass position, both A and B power is connected to the fuse blocks so the diode board can be safely removed. The Shorting board has an LED which is off when the board is in normal operational mode and is green when in the bypass mode of operation.
2.2.1.2 Alarms
The FAP provides visual alarms, by means of a lit LED, for a variety of status alarms.
Table 2-2 FAP Alarm Conditions
Alarm | Alarm Condition | Remote Indications |
---|---|---|
• EAGLE command through E5-TDM • E5-MDAL not present and E5-MDAL_P jumper off |
Dependent on EAGLE software |
|
EAGLE command through E5-TDM |
Dependent on EAGLE software |
|
EAGLE command through E5-TDM |
Dependent on EAGLE software |
|
Fuse LED |
• Distribution fuse blown • Alarm circuit board removed (no LED indication) • Jumper on the jumper circuit board is on • Power feed failure |
Fuse alarm to EAGLE through E5-TDM |
Power feed A is off, but power is available to B. |
Fuse alarm to EAGLE through E5-TDM |
|
Power feed B is off, but power is available to A. |
Fuse alarm to EAGLE through E5-TDM |
|
Shorting board in maintenance mode. |
Fuse alarm to EAGLE through E5-TDM |
A fuse alarm identifies the following problems or conditions within the FAP:
Use the following indicators to determine the nature of the problem:
Table 2-3 Additional Alarm Indicators
Indicator | Alarm Condition |
---|---|
Fuse alarm and fuse flag down |
Blown fuse |
Fuse alarm and PWR A LED |
Input power loss on A |
Fuse alarm and PWR B LED |
Input power loss on B |
Fuse alarm red and Shorting Board LED is green |
Shorting Board in maintenance mode (by-passing diodes) |
Fuse alarm red and Shorting Board LED is off |
Shorting Board in normal mode, blown fuse |
2.2.1.3 Diode Testing and the Shorting Board
The Diode Board must be tested periodically. To test the Diode Board without powering down the entire EAGLE, peform the following procedures.
2.2.1.3.1 Maintenance Mode
This section describes how to place the Shorting Board into maintenance (bypass) mode. Maintenance mode allows the removal of the Diode Board without taking down the system.
Procedure — Shorting Board Maintenance Mode
-
Check to verify the Shorting Board LED is not on, indicating the FAP is in normal mode.2.
-
Locate two screws securing the Shorting Board in its slot (see Figure 2-2). Note the orientation of the Shorting Board LED. Turn the screws at each corner of the board to the left until they disengage.
Figure 2-2 Shorting Board Faceplate, Normal Mode
-
Pull the board straight out of the FAP until the board is clear of the frame.
-
Turn the Shorting Board over and reinsert the board into its slot. Note the orientation of the Shorting Board LED (see Figure 2-3).
Figure 2-3 Shorting Board Faceplate, Maintenance Mode
The Shorting Board LED turns green and the fuse alarm LEDs turn red.
-
Ensure the board is seated properly and tighten the two screws to secure the board.
-
The Shorting Board is now in the maintenance (bypass) mode of operation.
2.2.1.3.2 Diode Board
This section describes how to remove and test the Diode Board.
Procedure — Remove the Diode Board
Use this procedure to remove the Diode Board for diode testing.
-
Check to verify the Shorting Board LED is on, indicating the FAP is in maintenance (bypass) mode.
-
Locate two screws securing the Diode Board in its slot. Turn the screws to the left until they disengage.
Figure 2-4 Diode Board Faceplate
-
Pull the board straight out of the FAP until the board is clear of the frame.
Procedure - Diode Testing
Use this procedure to test the power diodes on the Diode Board. A Digital Volt/Ohm Meter (DVM) with a Diode Setting is required. All testing is performed at the edge connector (J1) on the board.
Figure 2-5 Diode Board Edge Connector J1
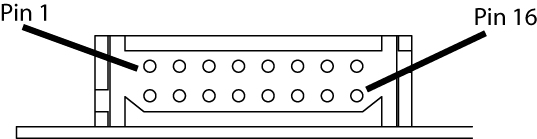
- Set the DVM to test diodes.
- Connect the DVM positive (+) lead and negative (-) lead to the pins indicated for each power diode.
Table 2-4 Power Diode Test Points
Diode J1 Pin Positive (+) Lead J1 Pin Negative (-) Lead CR1 #1
3
16
CR1 #2
6
16
CR2 #1
14
1
CR2 #2
11
1
CR3 #1
4
16
CR3 #2
5
16
CR4 #1
13
1
CR4 #2
12
1
The DVM should indicate a short circuit (>0.1V, <0.2V). Record the measurement.
- Reverse the leads.
The DVM should indicate an open circuit (OL). Record the measurement.
- If any measurements are in error, the diode board must be replaced.
- If the measurements are within acceptable parameters, reinstall the Diode Board.
2.2.1.3.3 Normal Mode
Use this procedure to place the Shorting board into normal mode. This mode of operation allows one bus to pick up the entire load when there is a loss of input power on the other bus.
Procedure — Shorting Board Normal Mode
-
Check to verify the Shorting Board LED is green, indicating the FAP is in maintenance mode.
-
Locate two screws securing the Shorting Board in its slot. Note the orientation of the Shorting Board LED (Figure 2-6). Turn the screws at each corner of the board to the left until they disengage.
Figure 2-6 Shorting Board Faceplate, Maintenance Mode
-
Pull the board straight out of the FAP until the board is clear of the frame.
-
Turn the Shorting Board over and reinsert the board into its slot. Note the orientation of the Shorting Board LED (see Figure 2-7).
Figure 2-7 Shorting Board Faceplate, Normal Mode
Note:
The Shorting Board LED is off and the fuse alarm LEDs turn green. -
Ensure the board is seated properly and tighten the two screws to secure the board.
-
The Shorting Board is now in the normal mode of operation.
2.2.2 3U FAP
The 3U FAP is a normal-profile unit that provides protected distribution of –48VDC power to the shelves in the frame. Allowing for the full population of a frame and for the failure of one primary supply, new installations of Control and Extension frames require two 60A feeds. The 3U FAP may be one of the following:
- 870-1606-01 (all revisions)
- 870-1616-02 with a revision G or lower
- 870-2320-01 with a revision B or lower
2.2.2.1 FAP Components
The FAP consists of nine printed circuit boards, each identified by an acronym on its label (see Figure 2-8):
-
Backplane (FAP_BP): Located inside the FAP unit, parallel to the back side of the FAP box.
-
Alarm board (FAP_AB): Located on the center-right of the front panel, set vertically inside the FAP unit, perpendicular to the front panel.
-
Diode boards (FAP_DB): Two boards located on the front panel, flanking the Alarm and Jumper boards on the left and right, and perpendicular to the front panel. Set vertically inside the FAP unit.
-
Extender boards (FAB-EB): Two boards located inside the FAP unit, parallel to the bottom of the FAP box, on the far right and left of the unit.
-
Fuse holder boards (FAP_FB): Two boards located inside and parallel to the front panel, on the far right and left of the FAP unit.
-
Jumper board (FAP_JB): Located on the center-left of the front panel, set vertically in the unit, perpendicular to the front panel.
Figure 2-8 Location of FAP Components
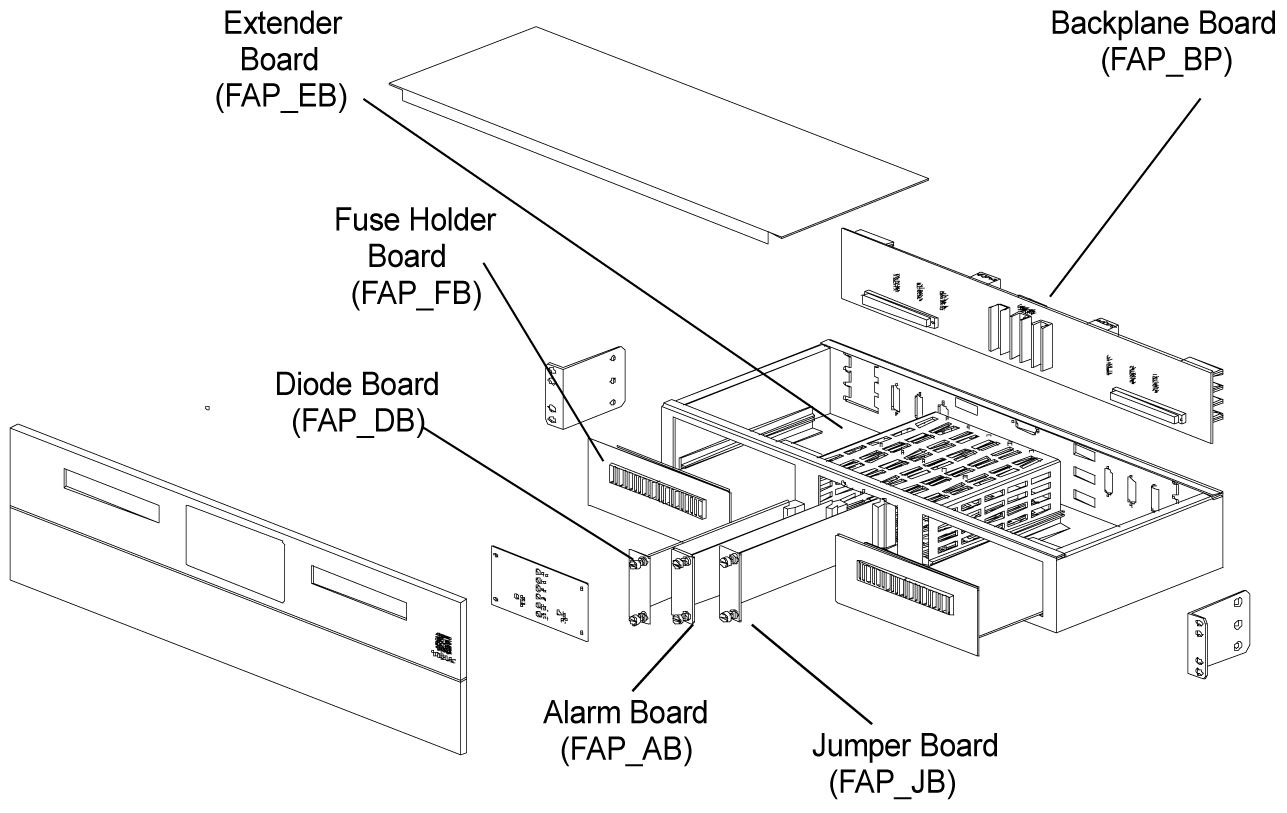
Each of the FAP components has associated functions.
Figure 2-9 FAP Component Functions
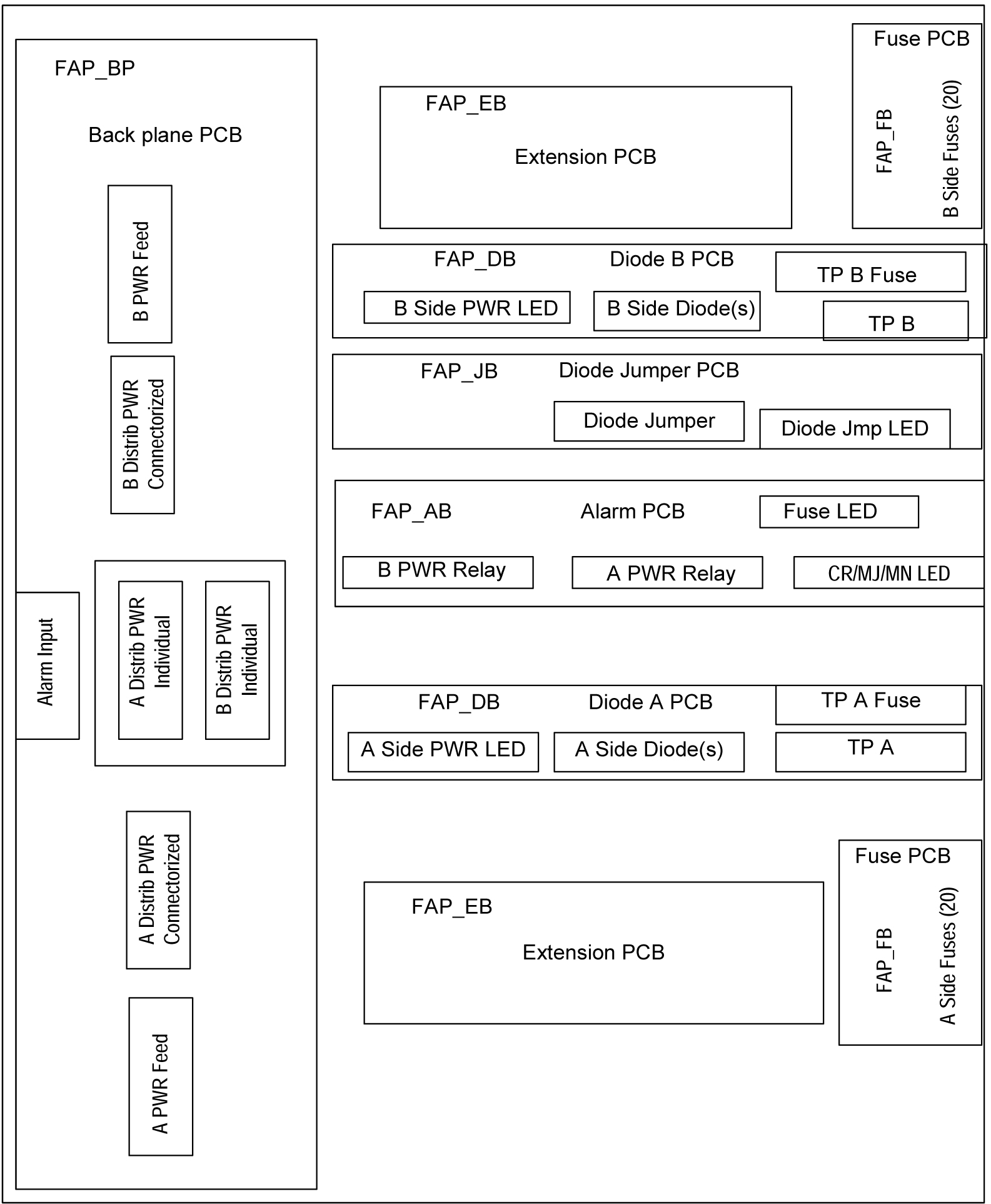
The FAP is composed of nine circuit boards. Eight of these circuit boards are field replaceable, and can be hot-swapped.
Table 2-5 FAP Component Replacement
Component | Replacement Requirements | Part Number |
---|---|---|
FAP Backplane (FAP_BP) |
Must be replaced through factory |
850-0515-xx |
FAPAlarm Board (FAP_AB) |
Field replaceable |
850-0518-xx (card) 870-1609-xx (assembly) |
FAP Diode Boards (FAP_DB_A and FAP_DB_B) |
Field replaceable (one at a time) |
850-0517-xx (card) 870-1608-xx (assembly) |
FAP Extender Boards (FAP_EB) |
Field replaceable (one at a time with service interruption) |
850-0519-xx |
FAP Fuse Holder Boards (FAP_FB) |
Field replaceable (one at a time with service interruption) |
850-0516-xx |
FAP Jumper Board (FAP_JB) |
Field replaceable |
850-0523-xx (card) 870-1641-xx (assembly) |
The following sections describe each type of circuit board:
Backplane Board (FAP_BP)
The backplane circuit board provides all of the external connections for the FAP. It consists primarily of circuit routing and connectors, but also has one pull-down resistor, which provides a default alarm signal for the Fuse Alarm in the event the alarm board is removed from the FAP.
Alarm Board (FAP_AB)
The alarm circuit board provides indicators and relays for the EAGLE status and fuse alarms. This board includes a jumper (JMP50) for future use. This jumper is installed for all existing configurations.
Diode Boards (FAP_DB)
The diode circuit boards provide power diodes and power input test points. Four diode footprints are included: two for Assembly A and two for Assembly B. Only one of the four positions is intended to be populated; the second footprint is provided for future part rating changes or additional heat-dissipation capabilities.
Extender Boards (FAP_EB)
The extender board provides connection between the backpanel board and the fuse holder boards.
Fuse Holder Boards (FAP_FB)
The fuse holder boards provide 20 fuses with a common alarm.
Jumper Board (FAP_JB)
The jumper board provides the capability to by-pass the diode boards with a fuse. Use this board only for maintenance operations.
2.2.2.2 Alarms
The FAP provides visual alarms, by means of a lit LED, for a variety of status alarms (see Table 2-6).
Table 2-6 FAP Alarm Conditions
Alarm | Alarm Condition | Remote Indications |
---|---|---|
• EAGLE command through E5-MCAP • E5-MDAL not present and E5-MDAL_P jumper off |
Dependent on EAGLE software |
|
EAGLE command through E5-MCAP |
Dependent on EAGLE software |
|
EAGLE command through E5-MCAP |
Dependent on EAGLE software |
|
Fuse LED |
• Distribution fuse blown • Alarm circuit board removed (no LED indication) • Jumper on the jumper circuit board is on • Power feed failure |
Fuse alarm to EAGLE through E5-MCAP |
Power feed A is off, but power is available to B. |
Fuse alarm to EAGLE through E5-MCAP |
|
Power feed B is off, but power is available to A. |
Fuse alarm to EAGLE through E5-MCAP |
|
Jumper on the jumper circuit board is on. |
Fuse alarm to EAGLE through E5-MCAP |
A fuse alarm identifies the following problems or conditions within the FAP:
Use the following indicators to determine the nature of the problem:
Table 2-7 Additional Alarm Indicators
Indicator | Alarm Condition |
---|---|
Fuse alarm and fuse flag down |
Blown fuse |
Fuse alarm and PWR A LED |
Input power loss on A |
Fuse alarm and PWR B LED |
Input power loss on B |
Fuse alarm and OP/MAINT LED is red |
Diode jumper is installed (by-passing diodes) |
2.2.2.3 Diode Testing and the Diode Jumper
The diode board must be tested periodically. To test a diode circuit board without powering down the entire EAGLE, perform the procedure listed in Table 2-8 for the corresponding FAP part number.
Table 2-8 FAP Part Numbers and Corresponding Procedures
Part Number | FAP Procedure |
---|---|
870-1606-01 (all revisions) |
Procedure 1 |
870-1616-02 revision G or lower |
Procedure 1 |
870-1606-02 revision H or higher |
Procedure 2 |
870-2320-01 revision B or lower |
Procedure 1 |
870-2320-01 revision C or higher (or 870-2320-03) |
Procedure 2 |
Procedure 1
This procedure to test a diode circuit board without powering down the entire EAGLE applies to the following FAPs:
-
870-1606-01 (all revisions)
-
870-1616-02 with a revision G or lower
-
870-2320-01 with a revision B or lower
-
Check to verify the OP/MAINT LED is green, indicating the FAP is not in maintenance mode.
-
Unscrew the two thumbscrews securing the FAP jumper board and remove the board.
-
On the jumper circuit board, move the jumper (the DB-26 male connector) from P71 to P72. Tighten the thumbscrews connecting the jumper to its mate, to ensure a good connection. This repositioning overrides the diodes, establishing a direct connection between input and fuse panels.
warning:
If fuses are blown, DO NOT continue with this procedure. Instead, contact My Oracle Support (MOS) at the appropriate number. -
Make sure the glass fuses are installed and verify they are “good” by using the multimeter to check for continuity across each of the glass fuses.
-
Verify that two glass fuses are behind the P72 connector. If these fuses are not present, install them before continuing.
-
Slide the jumper board back into the FAP and verify both of the following alarms display:
-
Locate diode board A and unscrew the two thumbscrews securing the board. Remove the board from the FAP.
-
Locate the diode to be tested. It has three pins and is attached to the large heat sink. The diode is labeled CR43.
-
Set your digital multimeter to measure resistance.
-
Measure the resistance between the center pin of the diode and either of the outside pins. Record this measurement.
-
Measure the resistance between these same pins again, but switch the multimeter leads, so the positive lead is now on the opposite pin. Record this measurement.
-
Compare the two measurements. If the diode is functioning properly, one reading should be less than 10K ohms and the other should be much greater.
If both readings are above or below 10K ohms, the diode may have failed. Replace the failed board with a spare diode board.
-
Repeat steps 9 through 11, measuring the resistance between the other outside pin and the center pin.
This completes the test for diode board A.
-
Repeat steps 6 through 12, using diode board B. This completes the test for diode board B.
-
Reinsert the two functional diode boards. Tighten the thumbscrews on each board to secure it to the FAP.
-
Unscrew the two thumbscrews securing the FAP jumper board and remove the board.
-
On the jumper circuit board, move the jumper (the DB-26 male connector) back from P72 to its original position on P71. Tighten the thumbscrews connecting the jumper to its mate, to ensure a good connection. This repositioning returns the diodes to their original, non-maintenance position.
-
Slide the jumper board back into the FAP. Verify the OP/MAINT LED lights green. The fuse alarm LED returns to green.
The diode board testing procedure is completed.
Procedure 2
This procedure to test a diode circuit board without powering down the entire EAGLE applies to the following FAPs:
-
870-1606-02 with revision H or higher
-
870-2320-01 with revision C or higher (or 870-2320-03)
2.3 Removable Drives
This section provides information about the removable drives associated with the EAGLE Maintenance Administration Subsystem Processor (MASP).
A removable drive is used for two purposes:
-
To hold an off-line, backup copy of the administered data and system GPLs
-
To hold a copy of the measurement tables
To use a removable drive to hold the system data, it must be formatted for system data. To use a removable drive to hold measurements data, it must be formatted for measurements data. The EAGLE provides the user the ability to format a removable drive for either of these purposes. A removable drive can be formatted on the EAGLE by using the format-disk
command. For more information on the format-disk
command refer to Commands User's Guide.
The USB storage media in the flush-mounted USB port of the MSP card is also used for backups. The dest=usb parameter is used to run the same.
2.3.1 Removable USB Drive
- Purpose:
- This section is referenced in this manual by many procedures requiring the use of the removable USB thumb disk in the E5-MASP card. The procedures found in this section are recommended procedures for handling the removable USB drive in the E5-MASP card.
- Requirements:
- None
Procedure - Remove USB Drive
2.3.2 Fixed SATA Drive
- Purpose:
- This section is referenced in this user's guide by many procedures requiring the use of the fixed SATA drive in the E5-MASP card. The procedures found in this section are recommended procedures for handling the fixed drive in the E5-MASP card.
- Requirements
-
- The new SATA Drives to be installed should be at the current system release.
- Before beginning this procedure, make sure there is a copy of the current release GPLs on a removable USB drive on-hand.
- System backups should be performed prior to the start of this procedure. Refer to Daily Procedures.
- You must be logged in to the EAGLE prior to performing this procedure.
Procedure - Remove Fixed SATA Drive
2.4 Daily Procedures
The procedures found in this section are recommended procedures for daily routine preventive maintenance. Some procedures may refer to other chapters within this document.
2.4.1 Backing Up the Database Daily
- Purpose:
- This procedure is used to make a backup of the database on the fixed disk and provide a current copy of the system data to be stored on-site. This procedure can then be used in the event a fixed disk is damaged. This procedure should not be confused with the other database archival procedures. Should the backup removable USB drive created with this procedure become unreadable, the other procedures in this chapter will ensure that a good copy of the database is still available.
- Requirements:
-
- The databases in the current partitions of both MASPs (FDCRNT) must be coherent.
- At least one removable USB drive formatted for system data is needed for this routine. Each removable USB drive should be labeled as “Daily Backup.” Each day, select the removable USB drive with this label and perform the backup procedure.
- Interval:
- Daily
Procedure - Backing Up the Database
2.4.2 System Reports Analysis
- Purpose:
- The purpose of this routine is to inspect the printer outputs for possible trouble messages and routinely check the status of the STP through traffic measurements. By inspecting printouts and measurements on a daily basis, system trends can be detected and resolved.
- Requirements:
- Printer must be configured to receive traffic reports. Measurements collection must be activated before reports containing current data can be printed. Enter the following command to activate measurements collection, if necessary:
chg-meas:collect=on
Refer to Commands User's Guide for more information. If measurements are already allowed, an error message indicates this.
2.4.3 Reports Description
- Purpose:
- This includes a system terminal and printer output system related messages as well as network protocol messages. Any abnormal activity (this is network dependent) should be highlighted and saved for later retrieval. Refer to Corrective Maintenance for a description of system related messages and procedures for recovery.
- Requirements:
- None
- Interval:
- Daily
- Variables:
- hh = The end half-hour interval (0 - 2330) for requested interval
Procedure - Print Report
2.4.4 File Transfer for LNP and INP Measurements
- Purpose:
- The purpose of this procedure is to output LNP/INP measurements to the file transfer area (FTA) so the measurements can be collected.
- Requirements:
- A computer with a VT320 or KSR connection to the EAGLE. A communication program that both emulates VT terminals and supports Kermit file transfer. Previous LNP/INP measurement files must have been successfully transferred and deleted (
dlt-fta
) before the start of this procedure. A spreadsheet program that can import Comma Separated Value (CSV) text files. A PC running ProComm© for Windows and Microsoft Excel© can also be used. - Interval:
- Daily and/or weekly.
Procedure - File Transfer
2.5 Weekly Procedures
The procedures found in this section are recommended for weekly routine preventive maintenance. Some procedures may refer to other chapters within this document.
2.5.1 Database Archive (Weekly)
- Purpose:
-
The purpose of this procedure is to create a copy of the database on a weekly basis over a period of four weeks to be stored in an archive. The copies can then be used in the event a removable USB drive is damaged, and a new copy is required. This routine will generate four copies of the database, all taken at weekly intervals.
Each tape in this cycle should be designated as Week 1, Week 2, Week 3, or Week 4. When all four removable USB drives have been used, repeat the process starting with the Week 1 USB drive.
- Requirements:
- Four removable USB drives formatted for system data are required for this routine. The removable USB drive should be labeled “Week 1” through “Week 4.” Once each week, select the removable USB drive with the appropriate label and perform the backup procedure. Each week, select the removable USB drive with the next sequential number and perform this procedure.
- Interval:
- Weekly
Procedure - Archive Database (Weekly)
2.5.2 Printer Inspection
- Purpose:
- This procedure verifies the printer is operational and the ribbon does not need replacement. Should the printer cease operation, system reports and trouble reports would not be printed at the system printer. Use the following procedure to verify the operation of the printer.
- Requirements:
- A printer connected through an RS232 to a serial port on the EAGLE control shelf backplane. Refer to the printer user manual (provided by the printer manufacturer) for detailed specifics on maintaining the printer.
- Interval:
- Weekly
- Variables:
- x = TDM serial port number (1-16)
Procedure -Printer Inspection
2.5.3 Remote Access Verification
- Purpose:
- The purpose of this routine is to verify proper operation of the modem used for remote access of the EAGLE system.
- Requirements:
- Remote terminal and modem.
- Interval
- Weekly
Procedure - Remote Access Verification
- From a remote PC or terminal, dial the telephone number of the modem connected to the Eagle.
- When connected, verify you are able to log in to the EAGLE system and enter commands.
- Once you have verified the operation of the modem, logoff from the EAGLE and terminate your connection.
2.6 Monthly Procedures
The procedures found in this section are recommended procedures for monthly routine preventive maintenance. Some procedures may refer to other chapters within this document.
2.6.1 Database Archive (Monthly)
- Purpose:
-
The purpose of this procedure is to create a copy of the database on a monthly basis over a period of four months to be stored in an archive. The copies can then be used in the event a removable USB drive is damaged, and a new copy is required. This routine will generate four copies of the database, all taken at monthly intervals.
Each tape in this cycle should be designated as Month 1, Month 2, Month 3, or Month 4. When all four removable USB drives have been used, repeat the process starting with the Month 1 USB drive.
- Requirements:
- Four removable USB drives formatted for system data are required for this routine. The removable USB drive should be labeled “Month 1” through “Month 4.” Once each month, select the removable USB drive with the appropriate label and perform the backup procedure. Each month, select the removable USB drive with the next sequential number and perform this procedure.
- Interval
- Monthly
Procedure - Database Archive (Monthly)
2.6.2 FAP Load Balance Verification (PN 870-0243-XX only)
- Purpose:
-
This procedure is used to verify the Load Balance Factor (LBF) for the A and B power supplied to each Fuse and Alarm Panel (FAP) in the EAGLE. This procedure applies ONLY to installed FAPs with P/N 870-0243-XX.
The LBF is an empirically derived number that provides an indication if a Oracle STP System Frame has an open power distribution diode. The difference in amperage between the “A” versus “B” battery leads should be within a “typical” range. Values outside of this range should be an indication of a potential problem and requires further investigation.
- Requirements:
- Oracle recommends that the verification be performed using a Clamping Type Multimeter (Clamp Amp Meter). If the Clamp Meter has different settings or functions than the ones described in this procedure, consult the instruction manual for this meter and determine substitute settings or functions. Results of this verification should be recorded on the form provided with this procedure and filed with the STP System maintenance records.
Caution:
This procedure must be performed with the utmost Caution. All safety precautions associated with in service equipment and power must be strictly followed. Any equipment that is below the shelf that is being worked on must be protected from falling tools or debris. All jewelry, rings, watches must be removed before this procedure is started. Read this procedure completely before proceeding. - Interval:
- Monthly
Procedure - FAP Load Balance
2.6.5 Cleaning Printer
- Purpose:
- The purpose of this routine is to prevent the system printer from building up dirt and dust around the print heads and carriage assemblies, preventing it from operating.
- Requirements:
- Printer cleaning kit, or cleaning solvent. Cotton swabs and damp cloth.
- Interval
- Monthly
Procedure - Clean Printer
- Follow the manufacturer’s procedures for cleaning the print head and carriage assembly.
2.7 Quarterly Procedures
The procedures found in this section are recommended procedures for quarterly routine preventive maintenance. Some procedures may refer to other chapters within this document.
2.7.1 Database Archive (Quarterly)
- Purpose:
- The purpose of this routine is to create an archive copy of the EAGLE database. This archive copy should be stored off-site and saved for emergency recovery when all other procedures have failed. This routine will reuse the same removable USB drive each quarter.
- Requirements
- This procedure requires a removable USB drive formatted for system data.
- Interval
- Quarterly
Procedure _Database Archive (Quarterly)
2.7.2 Preventing Dust Buildups
- Purpose:
- The purpose of this routine is to prevent dust build-up in and around the cabinet. Collection of dust within the EAGLE can allow electrostatic charges to build around circuit cards, possibly damaging cards installed in the system.
- Requirements:
- Damp cloth
- Interval:
- Quarterly
Procedure - Prevent Dust Buildup
2.7.3 Rectifier Voltage Inspection/Recording
- Purpose:
- The purpose of this routine is to verify that the rectifier is providing adequate voltages and has not become a marginal supply. By identifying power supply problems early, the possibility of failure can be circumvented.
- Requirements:
- Volt meter capable of measuring DC voltages in the range of -20VDC to -60VDC.
- Interval
- Quarterly
Procedure - Rectifier Voltage Inspection